Call us: 9054687723
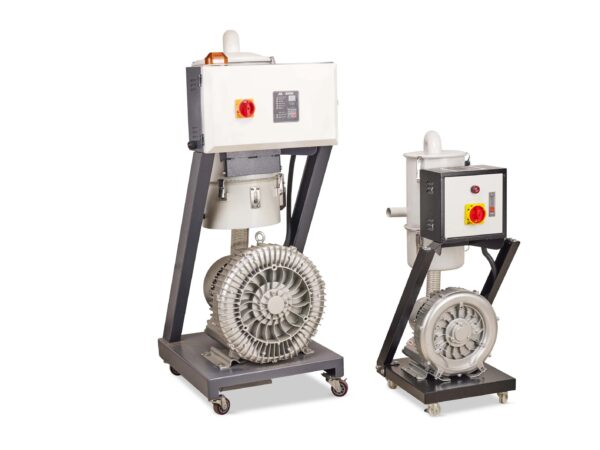
Vacuum Loader Conveying System
Our Vacuum Loader Conveying Systems are engineered for efficient and dust-free transportation of bulk materials across industries. Designed for seamless material handling, these systems enhance productivity and ensure smooth operation in your production line. Explore the best solutions at VR Brother’s Industries.
Vacuum Loader Conveying System
Vacuum Loader Conveying System and a pneumatic conveying system are two different methods used for transporting materials in industrial processes. Here’s a description of each:
1. Vacuum Loader Conveying System:
A Vacuum Loader Conveying System, also known as a vacuum transport system or pneumatic vacuum system, is a method of material handling that uses a vacuum to transport materials from one location to another. It operates by creating a pressure differential, with lower pressure at the destination point compared to the source point. The system typically consists of the following components:
– Vacuum Pump: A vacuum pump generates the suction force needed to create a pressure differential. It creates a vacuum by removing air or other gases from the conveying pipeline or vessel.
– Conveying Pipeline: The conveying pipeline is a closed system through which the materials are transported. It is designed to maintain airtight conditions to enable efficient vacuum operation.
– Material Receiver: The material receiver is the destination point where the materials are collected. It can be a hopper, silo, or another container designed to receive and store the conveyed materials.
– Filters and Separators: Vacuum conveying systems often include filters and separators to remove any dust or contaminants from the conveyed materials before they reach the material receiver.
Vacuum conveying systems are commonly used in industries such as pharmaceuticals, food processing, plastics, and chemical manufacturing. They are suitable for handling a wide range of materials, including powders, granules, pellets, and other bulk solids.
2. Pneumatic Conveying System:
A pneumatic conveying system is another method of material handling that uses compressed air or a gas to transport materials from one place to another. It operates by creating a high-velocity stream of air or gas that carries the materials through a pipeline. The system typically consists of the following components:
– Air Compressor: An air compressor provides the compressed air or gas needed to generate the conveying force. The compressor pressurizes the air or gas before it enters the conveying pipeline.
– Conveying Pipeline: The conveying pipeline is a closed system through which the materials are transported. It is designed to maintain the appropriate air or gas velocity for efficient conveying.
– Material Receiver: Similar to the vacuum conveying system, the material receiver is the destination point where the materials are collected.
– Filters and Separators: Pneumatic conveying systems may include filters and separators to remove any contaminants or fines from the conveyed materials before they reach the material receiver.
Pneumatic conveying systems are widely used in industries such as cement, mining, agriculture, and chemical processing. They can handle a variety of materials, including dry powders, grains, pellets, and even liquids in some cases.
Both vacuum conveying systems and pneumatic conveying systems offer efficient and flexible methods for transporting materials in industrial processes, each with its own advantages and considerations based on the specific requirements of the application.
Product Feature
Vacuum conveying systems offer several features that make them efficient and reliable for material handling in various industrial applications. Here are some key features of vacuum conveying systems:
1. Vacuum Generation: Vacuum conveying systems are equipped with powerful vacuum pumps that create the necessary suction force to transport materials. The pumps are designed to generate sufficient vacuum levels for efficient conveying while maintaining a stable and consistent airflow.
2. Material Flexibility: Vacuum conveying systems can handle a wide range of materials, including powders, granules, pellets, and other bulk solids. They are versatile and can transport materials with different particle sizes, densities, and characteristics.
3. Customizable Design: Vacuum conveying systems can be customized to suit specific application requirements. The system’s design can be tailored to accommodate the desired conveying capacity, distance, and the nature of the materials being transported. This allows for optimal performance and efficiency.
4. Closed System: Vacuum conveying systems operate in a closed system, ensuring minimal dust or material leakage during the conveying process. This feature is particularly beneficial in industries where containment and hygiene are crucial, such as pharmaceuticals or food processing.
5. Multiple Pick-up and Discharge Points: Vacuum conveying systems can be designed with multiple pick-up points and discharge points. This allows for efficient and flexible material transfer from various sources to different destinations within a production facility.
6. Automated Operation: Vacuum conveying systems can be integrated with automation and control systems for seamless operation. They can be programmed to start and stop automatically based on specific triggers or set operational parameters, reducing manual intervention and ensuring consistent performance.
7. Monitoring and Safety Features: Many vacuum conveying systems are equipped with monitoring sensors and safety features. These can include pressure sensors, level detectors, filter monitoring systems, and alarms to ensure safe and reliable operation and prevent equipment damage or material spillage.
8. Easy Maintenance and Cleaning: Vacuum conveying systems are designed for ease of maintenance and cleaning. They often have quick-release clamps or access doors for convenient inspection, cleaning, and maintenance tasks. This helps in maintaining system performance and hygiene standards.
These features contribute to the efficiency, reliability, and versatility of vacuum conveying systems, making them a popular choice for material handling in industries where controlled and dust-free transport is essential.
Product Application
Vacuum conveying systems find a wide range of applications across various industries where the efficient and dust-free transfer of materials is crucial. Here are some common applications of vacuum conveying systems:
1. Pharmaceuticals: Vacuum conveying systems are extensively used in the pharmaceutical industry for the transfer of powders, granules, and other materials. They are employed in processes such as tablet compression, blending, coating, and filling operations, ensuring contamination-free material transfer and maintaining a sterile environment.
2. Food Processing: Vacuum conveying systems are widely utilized in the food processing industry for the handling of ingredients, powders, spices, and additives. They are used in processes like mixing, batching, filling, and packaging, where maintaining food safety and preventing cross-contamination are essential.
3. Chemical and Petrochemical: Vacuum conveying systems are employed in the chemical and petrochemical industries for the transport of various powders, granules, and bulk solids. They are utilized in applications such as material transfer between different processing stages, blending, and packaging.
4. Plastics and Rubber: Vacuum conveying systems are used in the plastics and rubber industries for the transport of plastic pellets, powders, and other materials. They are commonly employed in extrusion processes, injection molding, compounding, and recycling operations.
5. Cosmetics and Personal Care: Vacuum conveying systems are utilized in the cosmetics and personal care industry for the transfer of powders, pigments, and ingredients. They are employed in processes such as blending, mixing, and packaging of cosmetic products.
6. Printing and Packaging: Vacuum conveying systems find application in the printing and packaging industry for the handling of paper, cartons, labels, and other materials. They are used to transfer materials between different stages of printing, packaging, and labeling operations.
7. Ceramic and Glass: Vacuum conveying systems are employed in the ceramic and glass industries for the transport of powders, granules, and raw materials. They are used in processes such as mixing, grinding, kiln feeding, and packaging.
8. Automotive and Aerospace: Vacuum conveying systems find application in the automotive and aerospace industries for the handling of powders, abrasive materials, and components. They are used in processes like paint spraying, abrasive blasting, and material transfer in manufacturing operations.
These are just a few examples of how vacuum conveying systems are utilized in different industries. Their ability to ensure efficient and dust-free material transfer makes them essential in applications where cleanliness, contamination control, and operational efficiency are critical.
Reviews
There are no reviews yet.